Lubricant Management for Reliability Improvement
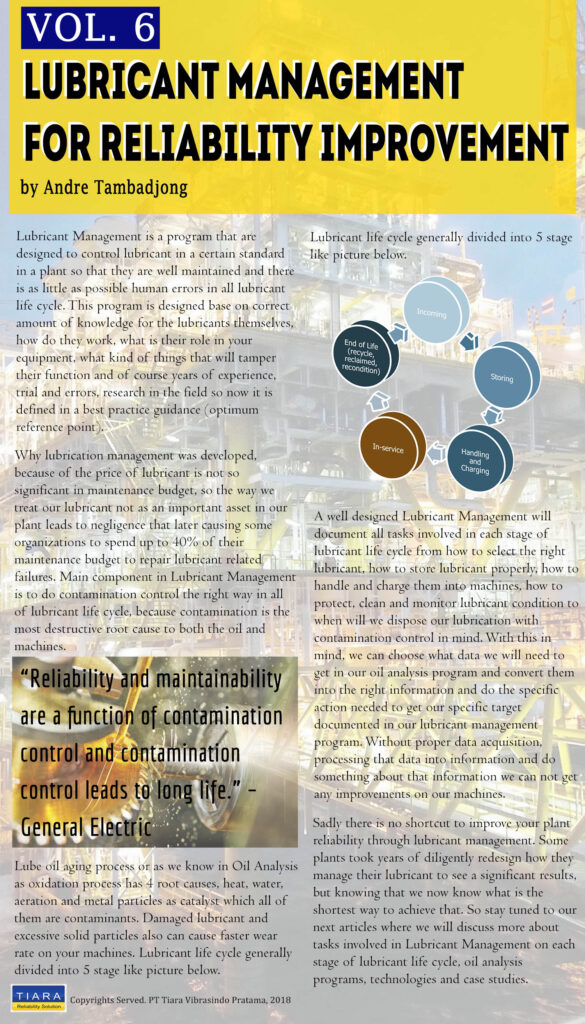
What is Lubricant Management?
Lubricant Management is a program that are designed to control lubricant in a certain standard in a plant so that they are well maintained and there is as little as possible human errors in all lubricant life cycle. This program is designed base on correct amount of knowledge for the lubricants themselves, how do they work, what is their role in your equipment, what kind of things that will tamper their function and of course years of experience, trial and errors, research in the field so now it is defined in a best practice guidance (optimum reference point).
Why lubrication management was developed, because of the price of lubricant is not so significant in maintenance budget, so the way we treat our lubricant not as an important asset in our plant leads to negligence that later causing some organizations to spend up to 40% of their maintenance budget to repair lubricant related failures. Main component in Lubricant Management is to do contamination control the right way in all of lubricant life cycle, because contamination is the most destructive root cause to both the oil and machines.
Lube oil aging process or as we know in Oil Analysis as oxidation process has 4 root causes, heat, water, aeration and metal particles as catalyst which all of them are contaminants. Damaged lubricant and excessive solid particles also can cause faster wear rate on your machines.
“Reliability and maintainability are a function of contamination control and contamination control leads to long life.” – General Electric
Lubricant life cycle generally divided into 5 stage like picture below.
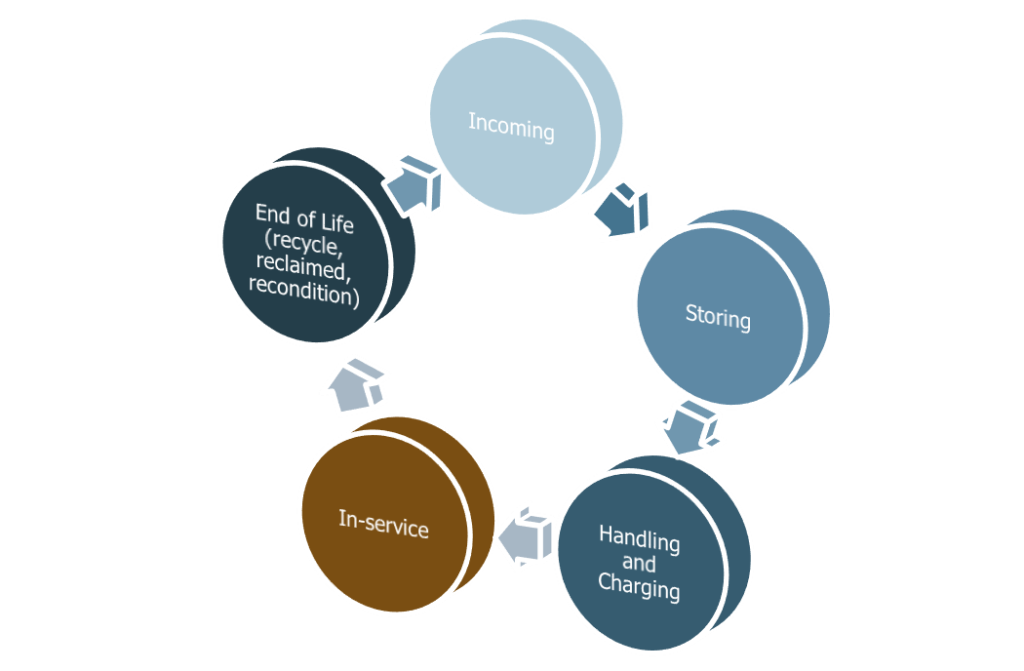
A well designed Lubricant Management will document all tasks involved in each stage of lubricant life cycle from how to select the right lubricant, how to store lubricant properly, how to handle and charge them into machines, how to protect, clean and monitor lubricant condition to when will we dispose our lubrication with contamination control in mind. With this in mind, we can choose what data we will need to get in our oil analysis program and convert them into the right information and do the specific action needed to get our specific target documented in our lubricant management program. Without proper data acquisition, processing that data into information and do something about that information we can not get any improvements on our machines.
Sadly there is no shortcut to improve your plant reliability through lubricant management. Some plants took years of diligently redesign how they manage their lubricant to see a significant results, but knowing that we now know what is the shortest way to achieve that. So stay tuned to our next articles where we will discuss more about tasks involved in Lubricant Management on each stage of lubricant life cycle, oil analysis programs, technologies and case studies.